There are many savings to be made by assessing your packaging supply line. The closer you look, the easier it is for you to lower your packaging expenses. But it’s important to remember the fine line between saving money and cost-cutting. Saving money is what you’re after, whereas cost-cutting ends up being more expensive in the long run.
Getting your product to its destination safely and securely is a valuable investment, making compromises in these areas only leads to lost or damaged shipments. What you save, you will end up spending on replacement orders.
Here are some tips to reduce your packaging costs without compromising quality:
1- Bulk Purchasing: Save with Quantity
Ordering packaging materials in bulk often comes with substantial discounts. By accurately forecasting your needs and buying supplies in large quantities, you can significantly reduce per-unit costs.
Also, building a long-term relationship with suppliers can lead to better deals and exclusive discounts.
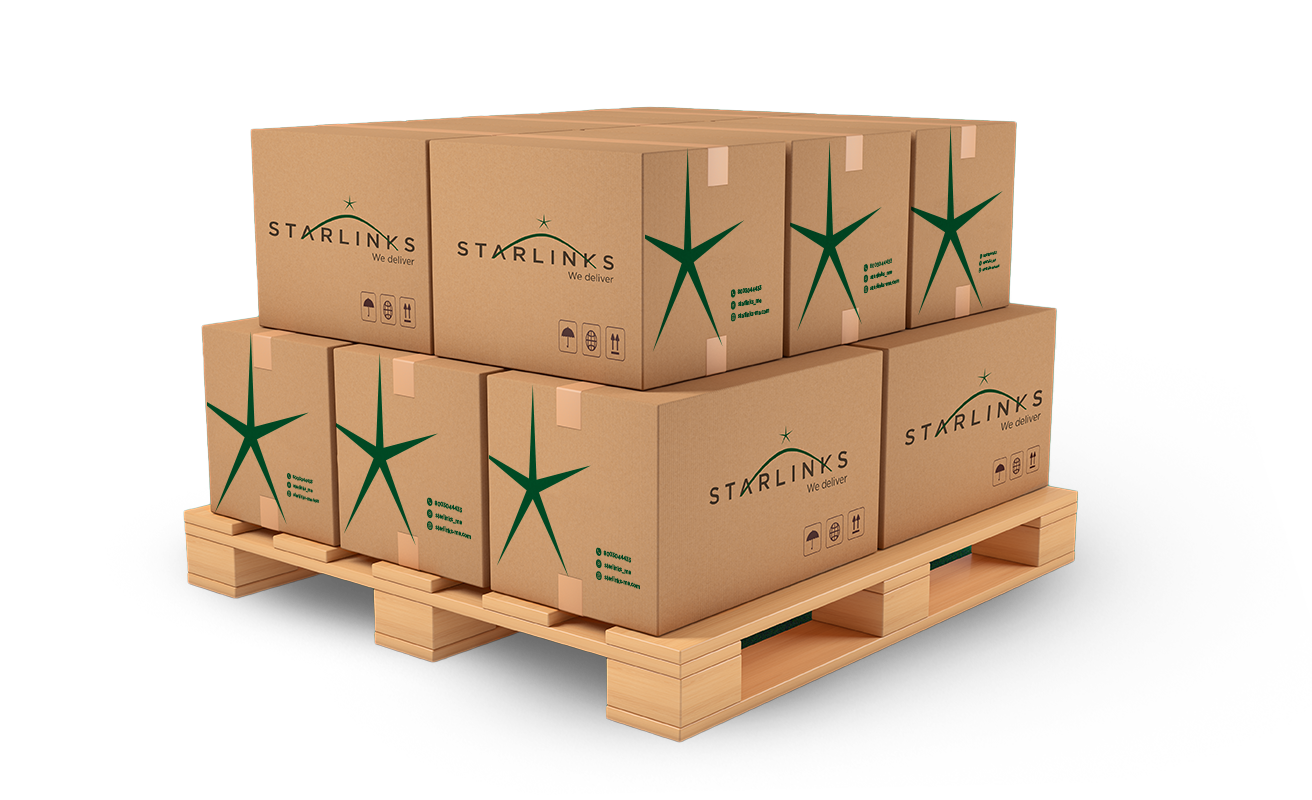
2- Custom-Sized Packaging: Eliminate Waste
Buying standard boxes that don’t fit your product will lead to wasted material, wasted space, excess weight, and more money down the drain. Also, oversized packaging takes up more space during delivery.
So, the perfect solution here is to customize your packaging specifically for your product; there’s as little material used as possible. Also, packaging that fits your product perfectly ensures efficient use of delivery space and less shelf space.
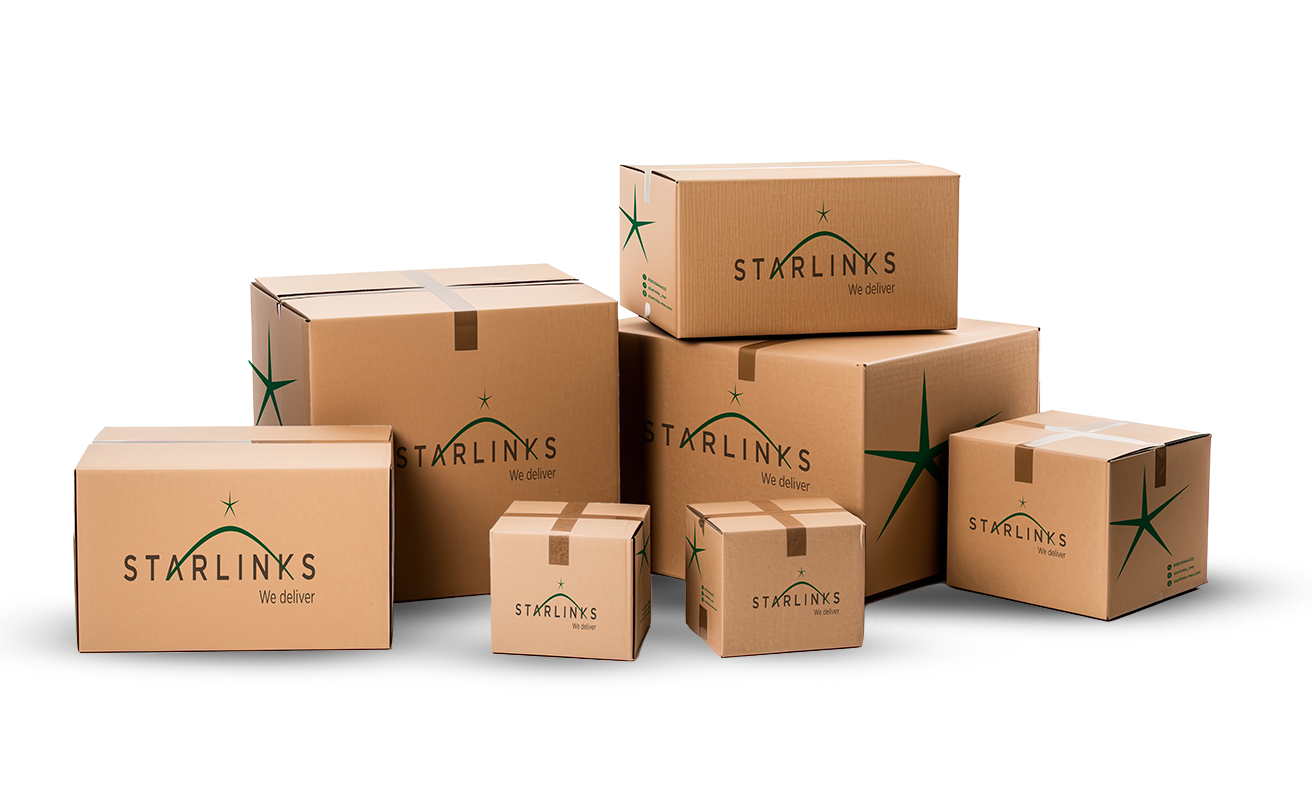
3- Custom Insert: Enhance Safety and Unboxing Experience
Void filler is often impractical and adds unnecessary expense. Unless you’re shipping an oddly shaped product and your packaging design has already been optimized, the use of a void filler is inescapable.
Custom inserts are designed to hold your products in place, eliminating the need for void fillers.
They not only enhance the unboxing experience but also add extra security.
A custom insert for every product also means that you can use a standard, off-the-shelf box without compromising security.
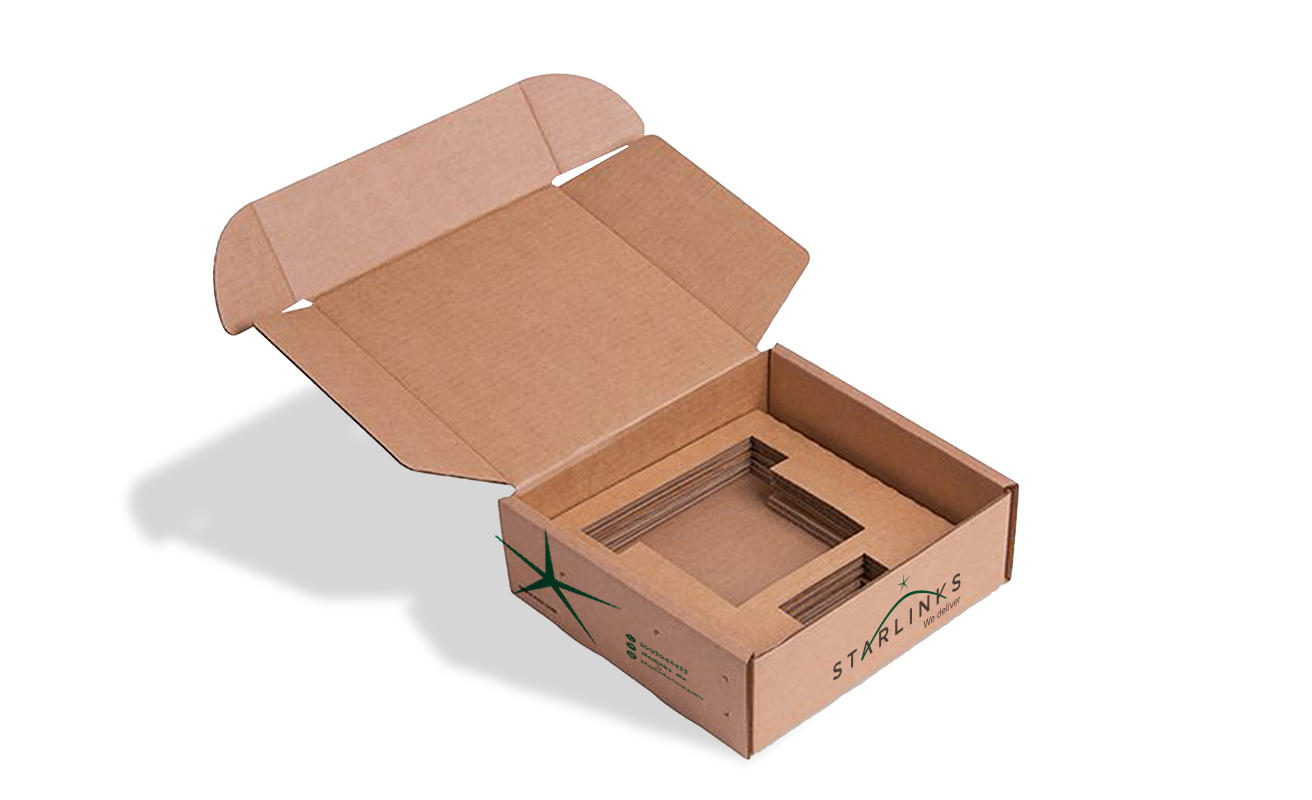
4- Lower your assembly & packing time:
Reducing the per-unit packaging time is an effective way to reduce the ongoing costs.
Adding packaging tape, either to seal the boxes or add strength is not only time-consuming but uses another consumable product. This is where the extra costs are often hidden.
Quality packaging design means the need for less tape, we can solve this by using the “self-locking mechanism boxes”.
Products like self-locking boxes come pre-glued and simply need to be expanded to automatically lock into place, so it will save you a lot of time.
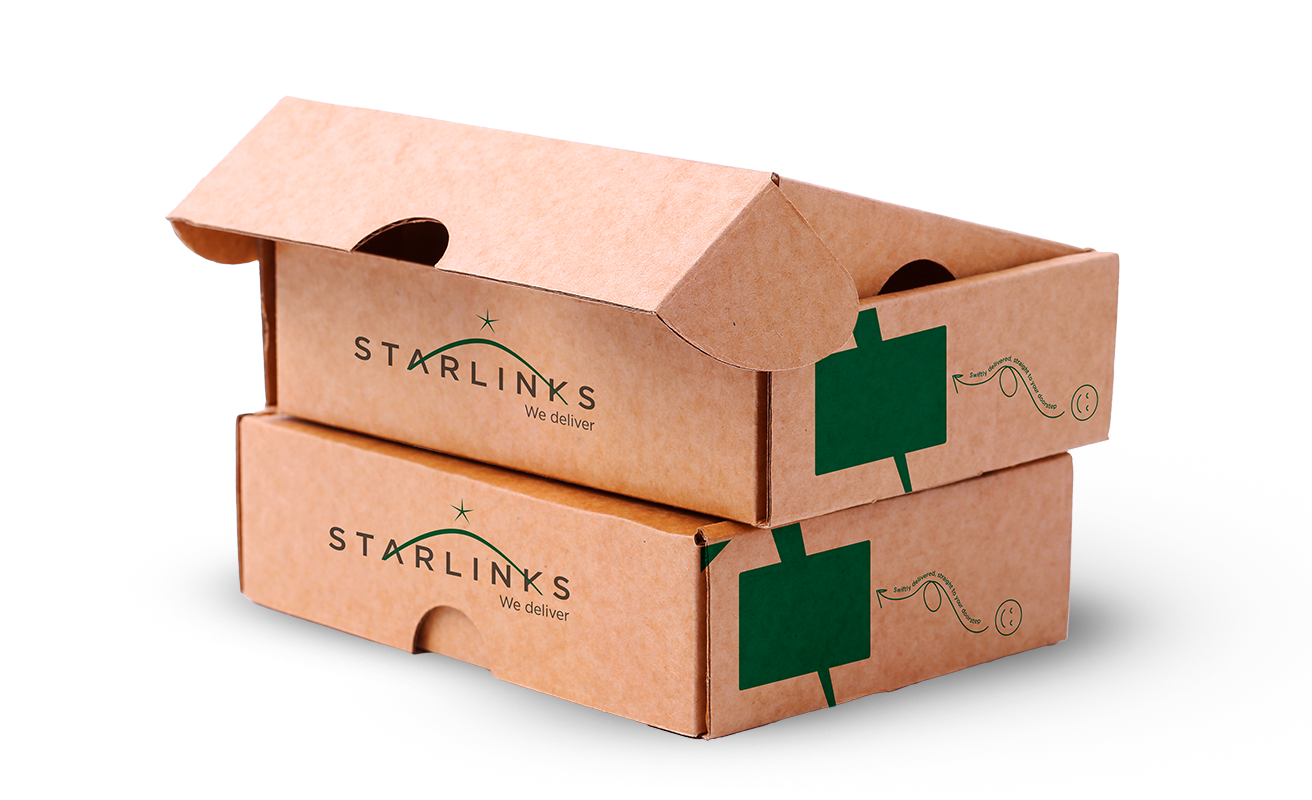
5- Reduce Packaging Weight & Size:
You pay a delivery fee based on either the size or weight of your packages. So, any savings made in reducing the size and weight of the packaging are savings in your back pocket.
Most likely your products’ packaging is going to be made of paperboard. Depending on the products’ handling demands, the thickness of the box may be able to be reduced. You may be surprised at how thin you can go and still be protecting your product.
Also, products that come in their own packaging are often durable on their own. This means that they don’t need an extra box for the purpose of being delivered to the final consumer. In this situation, a mailing bag is a great option to implement.
Most forms of mailing bags are flexible, waterproof, and add a fair amount of protection without the weight.
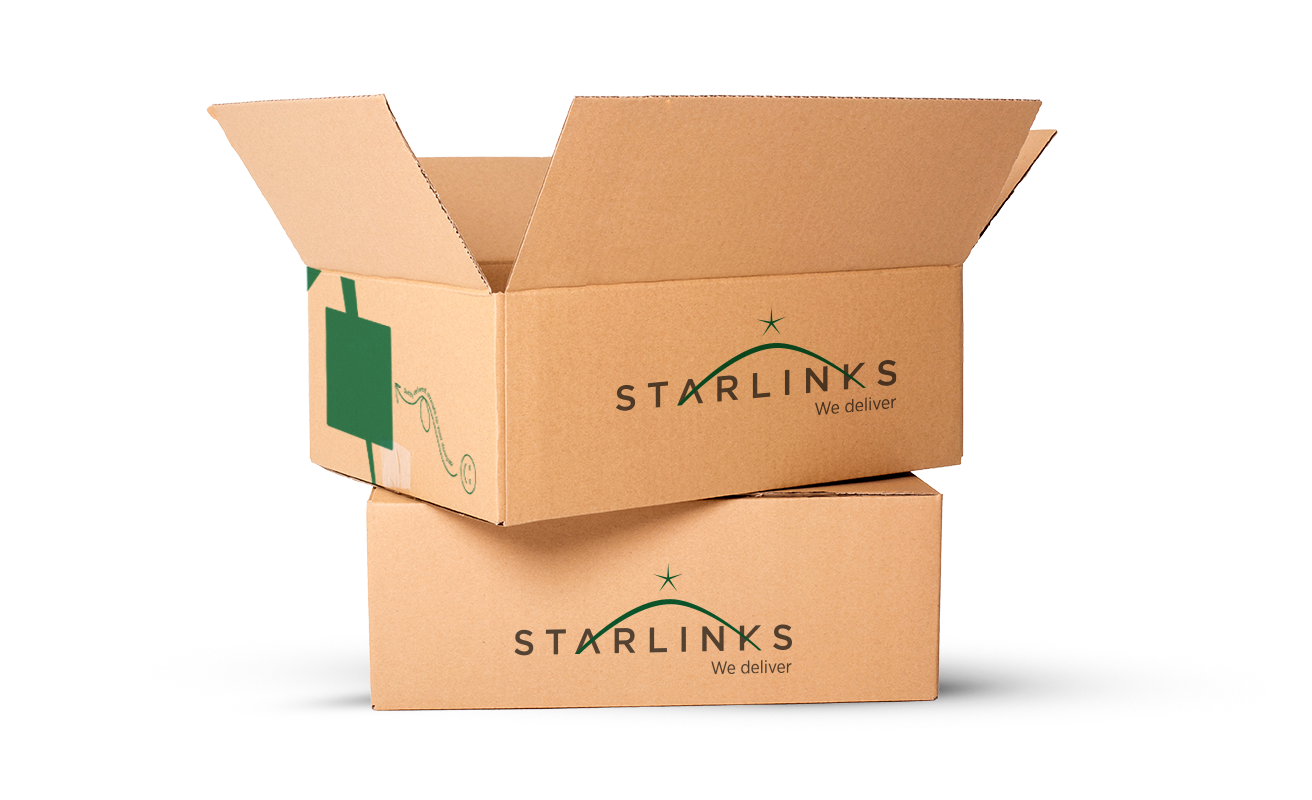
6- Reduce your number of suppliers:
Sourcing products from several different vendors is a great way to burn cash and increase problems, Even the slightest change to design means you have to:
- Contact multiple suppliers.
- Check if every supplier can meet the requirements.
Using a single vendor eliminates these needs.
A single supplier lowers the chances of mistakes that are often both costly and time-consuming to rectify.
This not only saves you the hassle of contacting multiple suppliers but can help you cut off extra delivery costs.
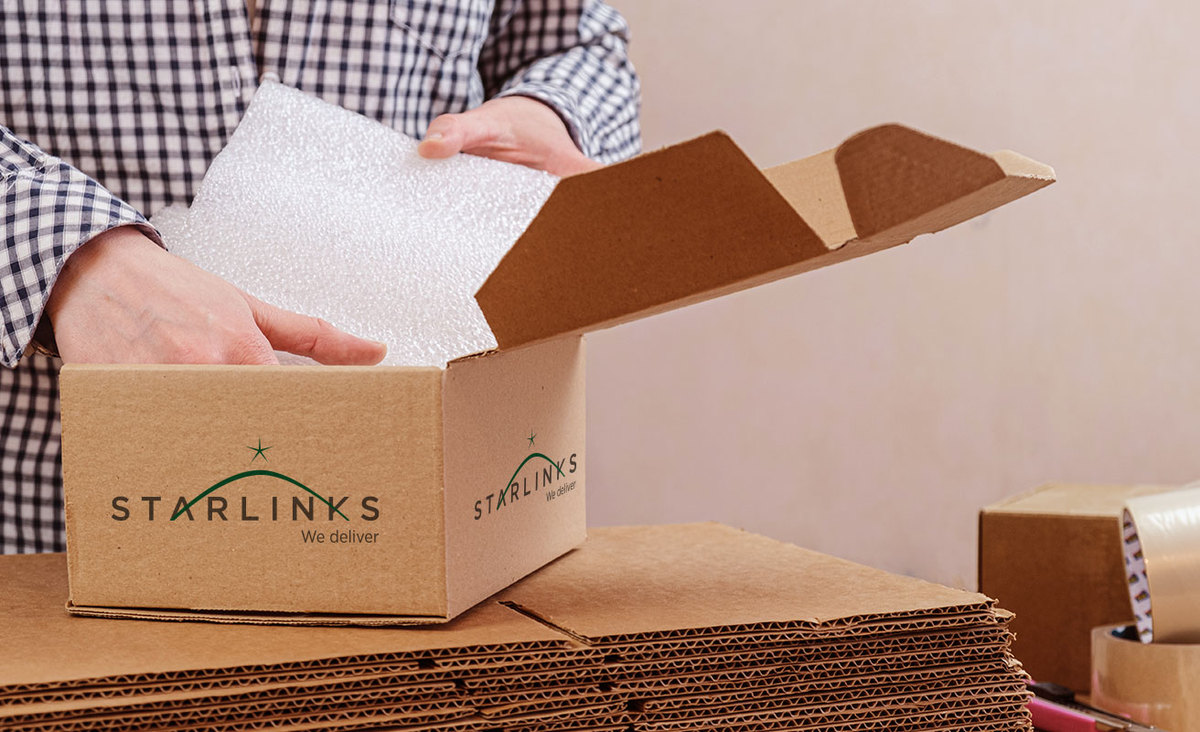
7- Follow stock closer:
Too much stock ties up money on your shelves, and not enough leads to shortages and delays in fulfilling orders. That’s why you must know exactly when to reorder your packaging and know its lead times. So, working with a vendor that has set production and delivery times means that you know exactly how far in advance to order your packaging.
Using an inventory management system that can automatically place an order for packaging when you reach the minimum threshold. Such software means that you will spend less time manually counting stock numbers, and you’re always aware of what’s at hand. With a closer eye on stock numbers, you can tie up less capital on shelves, and make the most use of the space you’ve got.
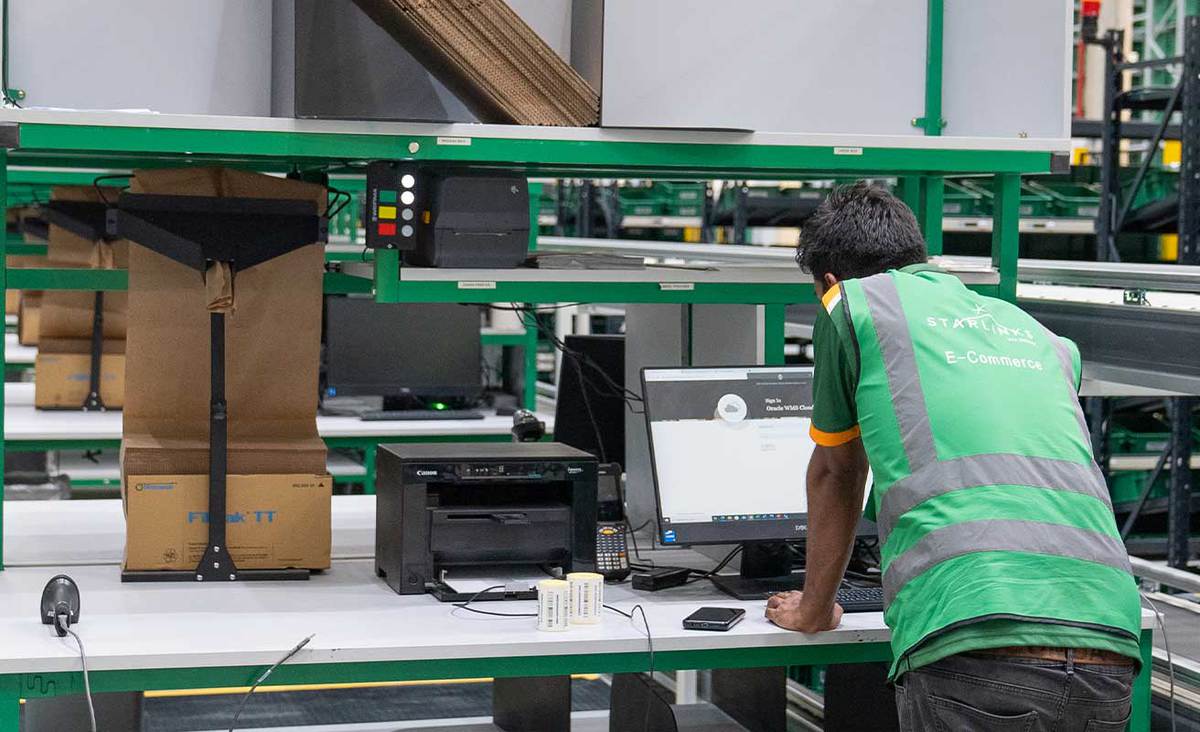
Reducing your packaging expenses doesn't require completely reimagining the process or adopting the latest technology. By optimizing your current methods and customizing solutions to suit your unique needs, you can achieve significant cost savings. Start implementing these strategies today to reduce your packaging costs while maintaining the quality and safety of your products.